Paper Feeding Technology: Understanding the Friction Feed Method
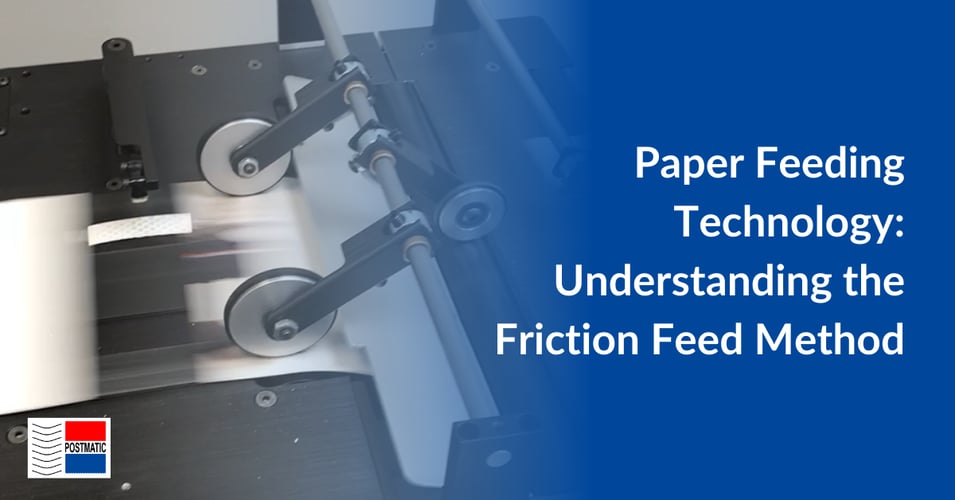
Table of Contents
The friction feeder plays a crucial role in the automation of tasks in the printing and paper handling industry, helping to save both time and resources. This advanced technology is particularly effective at handling flat products through a technique known as friction feed.
What Is Paper Feeding Technology?
Paper feeding technology encompasses the various methods to move paper through devices like printers and feeders.
Comparing Paper Feeding Technologies
- Friction Feed: Simple and versatile, this method is ideal for a wide range of applications. It works by using friction to move paper or materials through a machine, which ensures reliable performance in various printing and feeding tasks. It is the preferred choice in environments where reliability and low maintenance are a priority.
- Vacuum Feed: This system uses suction to pull delicate papers through the machine, which makes it particularly suitable for lightweight and fragile materials. Its gentle handling means even the most sensitive papers remain undamaged during the feeding process.
- Belt Feed: Known for its efficiency in high-speed operations, the belt feed method enables the rapid movement of materials. However, it is more complex than other feeding systems, requiring precise alignment and maintenance to ensure optimal performance and prevent jams during operation.
What Is the Meaning of Friction Feed?
Friction feed refers to the process where paper is moved along a path via friction created by rubber or silicone rollers.
Machines where high precision is necessary often use this method to avoid complex mechanical or vacuum feeders. The friction feed method allows for quick adjustments and reduces the risk of misfeeds.
What Is the Function of the Paper Feeder?
The primary function of a paper feeder is to ensure smooth and continuous feeding of paper into a machine to prevent jams and ensure quality output. In friction feeders, the paper feed mechanism's role sets the pace and maintains alignment for accurate processing.
Advantages of a Reliable Paper Feeder
- Efficiency: Maximizes throughput by reducing manual intervention.
- Precision: Ensures correct alignment, critical for tasks like printing and mailing.
- Productivity: Minimizes interruptions, allowing for more consistent operation.
How Does a Friction Feeder Work?
A friction feeder moves paper through a series of rollers that create friction.
This process begins with the operator loading a stack of paper into the feeder's hopper. The rollers then engage with the top sheet, generating just enough friction to separate it from the stack and move it forward. The control systems within the feeder carefully regulate roller pressure and speed to match the paper type. These adjustments are critical for maintaining the precise separation and feeding of sheets, which reduces the risk of jams and ensures smooth operation.
Friction feeders are equipped with advanced sensors that detect any irregularities in paper feed, such as skewed alignment or double-feeding. These sensors communicate with the control systems to make real-time adjustments. Maintenance of these systems is crucial, as clean and well-calibrated components significantly enhance the feeder's reliability and longevity.
Steps in the Friction Feed Process
- Loading: Paper is loaded into the feeder's tray.
- Feeding: Rollers engage, creating friction to move the paper.
- Output: The paper exits the feeder, ready for the next stage of processing.
What Is the Friction Feed Method on Paper?
The friction feed method moves sheets of paper through a printer or other machinery. It's commonly found in printers, feeders, and other devices that require precise paper handling.
What Is the Paper Feed Mechanism on a Printer?
The friction feed method relies on rollers that grip and pull the paper along its path. Unlike vacuum or suction mechanisms, friction feed is both cost effective and easy to maintain, making it a favorite in many office environments.
The effectiveness of the friction feed method largely depends on the quality and maintenance of its components. High-quality rubber rollers are crucial for ensuring consistent grip, especially when handling varying types of paper stock. These rollers need regular inspections and cleaning to prevent slippage, which could result in paper jams or misalignment. Proper maintenance not only extends the lifespan of the equipment but also ensures the feed mechanism operates smoothly, which minimizes downtime and maximizes productivity.
Despite its many advantages, the friction feed method does have limitations. It may be unsuitable for handling highly-glossy or thick paper types, as these are often difficult for the rollers to grip. Additionally, variations in paper thickness or surface texture may pose challenges, potentially leading to feed errors or damage to the paper. However, advancements in friction feed technology continue to address these issues by incorporating adjustable pressure features and improved materials to better accommodate a range of paper types. This expands its use across different printing and paper-handling applications.
Benefits of the Friction Feed Method
The friction feed method offers several advantages over other methods, including:
- Simplicity: The minimalistic design reduces mechanical complexity, which means fewer breakdowns and less downtime.
- Versatility: Friction feed technology is adaptable to a wide variety of paper stocks, sizes, and weights.
- Cost effectiveness: Compared to other paper feeding methods, friction feed is more affordable and still offers high precision.
- Efficiency: Its capability to handle large batches of paper at once enables the friction feed method to offer continuous processing without the need for frequent reloading or manual intervention.
- Speed and Precision: The rollers' gripping action ensures consistent paper alignment, which leads to accurate printing results, even at high speeds.
What Is the Paper Feeding Mechanism?
The paper feeding mechanism features multiple components that work together to transport paper from one section of a machine to another.
In friction feeders, this mechanism controls speed, alignment, and pressure to ensure precise paper handling.
What Is the Friction Feed Mechanism?
This detailed guide (PDF) provides maintenance tips and insights into the inner workings of these machines.
Key Components of the Paper Feeding Mechanism
- Feed Rollers: Grip and move the paper.
- Sensors: Detect the presence of paper and its alignment.
- Control Systems: Adjust speed and pressure settings for optimal performance.
Applications of Friction Feed Technology
The versatility of friction feeding technology makes it suitable for a diverse range of industries and applications. Some common uses include:
- Printing and Packaging: Friction feeders are common in the printing and packaging industry for tasks such as labeling, coding, and inserting promotional materials into product packages.
- Mailing Systems: In mailrooms, friction feed technology automates the collation and insertion of documents into envelopes.
- Banking and Finance: Banks use friction feeders to process checks, deposit slips, loan applications, and other financial documents.
- Pharmaceuticals: The pharmaceutical industry relies on friction-feeding systems for accurate counting and packaging of tablets, capsules, and other medications.
- Food Industry: Food manufacturers also benefit from friction feed technology in packaging and labeling processes, which ensures consistent production.
In Conclusion
The friction feeder plays an indispensable role in modern printing, mailing, and packaging industries. Understanding the friction feed method on paper provides valuable insights into optimizing efficiency and productivity. Investing in a reliable friction-feeding system will bring significant benefits to businesses looking to enhance their operations.
Ready to optimize your operations with cutting-edge paper-feeding technology? Explore our range of friction feeders and discover a tailor-made solution for your business needs.